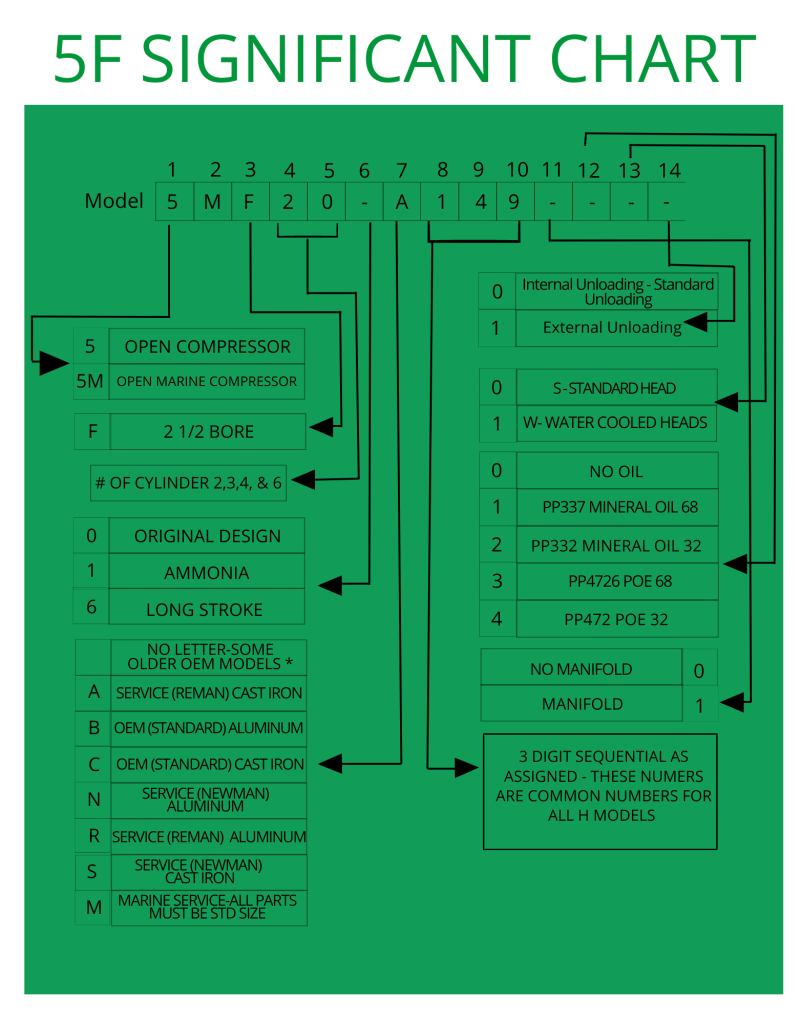
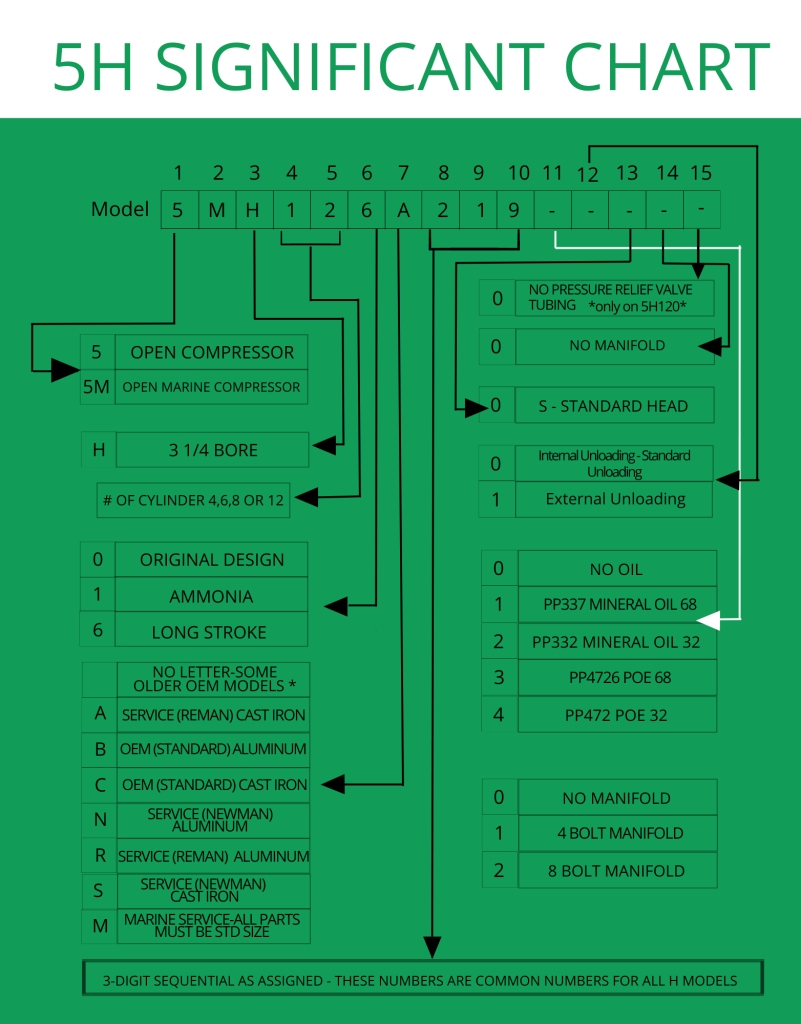
May 27, 2014
A-1 How To Series. Wiring a Carrier 06E compressor for Part Wind Start.
Thanks for watching. Call us at 800 743-6009 if you need any additional assistance.
April 15, 2014
A good PM program should include a complete review of the components in the refrigeration and/or HVAC system. The components should be cleaned, tested and functioned to ensure that the system will operate as intended. This system review should be performed at least annually. The benefits will be a smooth running system and a customer who will be yours for life.
For more information on developing a good PM program, call 1-800-743-6009.
April 15, 2014
Probably the most important thing to remember is a well maintained electrical system and correct Super Heat at the compressor as a rule will almost always prevent costly compressor failures
For more information on developing a good PM program, call 1-800-743-6009
April 15, 2014
Your compressor is now installed, run tested and charged. It seems to be running great but you need to be sure.
Remember, you only want to change the compressor once. So finding the reason for the failure is a must.
For more information on developing a good PM program, call 1-800-743-6009